Secrets of Top Performers
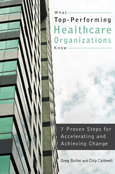
If every hospital starts the year with a strategic plan, budget and the desire to succeed, then what are the attributes that separate top performers from non-starters?
Why have many healthcare organization launched into Lean and Six Sigma only to be disappointed and abandon their efforts within one to two years because of a lack of acceptance and no tangible ROI for their efforts?
Key Findings:
-
Seeking Lean-Six Sigma training alone as the solution
A "Training Alone" approach is the number one reason for failure. Success requires comprehensive approach that is more than adding tools. It requires key structures for accountability, strategic focus, and a strong change model before meaningful gains can be achieved.
-
Understanding the 4 Non-Delegable Roles of Senior Leaders
Success starts with senior leaders understanding their four non-delegable roles in the performance improvement / quality process. Without their understanding and support, performance improvement activities seldom achieve strategic or sustainable results.
-
Hiring the "Expert"
Many senior leaders believe the solution is to hire an external Lean-Six Sigma expert into the organization. Sometimes they believe it requires someone from outside of healthcare to bring new thinking into the organization. Other times, they seek out a healthcare expert and believe that the expert can evangelize the organization to the new methods. The truth is that neither of these approaches has proven productive unless the proper accountability structure, change models, and senior leader strategies are in place. Only then are results both certain and sustainable.
-
Presence of Accountability Systems
The number one differentiator of success is the presence of a strong accountability system, which makes progress or its absence instantly visible to senior leaders and the rest of the organization. The presence of strong accountability structures, like our 100 Day Workout, are the number one factor determining success and directly correlates with the organization’s ability to execute their strategies with high proficiency.
-
Presence of a Uniform Change Model
Healthcare is notoriously bound by traditions and resistant to change. Success requires that senior leaders design and promote a uniform change-model capable of helping managers overcome their fears and implement change in an orderly process. Unfortunately, Six Sigma's DMAIC structure and Lean Kaizen Events are not designed to overcome resistance to change and enhance the speed of change.
-
Strategic Focus on Large Core Processes
One of the common pitfalls in the traditional deployment of Lean-Six Sigma is a project-by-project focus. This is true for two primary reasons. First, organizations that try to accomplish everything tend get nothing done. Second, when senior leaders delegate down the task of project selection and fail to focus the organization on meaningful processes, the result is a "project by project" or departmental approach, which seldom yields strategic results for the organization as a whole. For this reason, we advocate the Big Q Core process framework as the basis of project selection. This concept is a proven means of achieving focus on processes that matter.
-
Application of Industrial Lean-Six Sigma
The direct application of industrial Lean-Six Sigma frequently fails to gain traction in healthcare. First, the industrial jargon all too frequently reduces acceptance among clinicians and staff. It gets in the way rather than promotes understanding of the concepts. It is possible to eliminate industrial jargon and translate the tools to speak the "language of healthcare." The second is that manufacturing and healthcare have obvious differences. Where you will achieve meaningful gains in an industrial setting are very different from the healthcare environment.
-
Speed and a Bias to Action are Critical
Senior leaders in top performing organizations know that it is all about achieving speed in implementation. It is about ending the debate and never ending desire for more analysis and getting people to take action on what they do know. Unfortunately, it is possible for the traditional approach to Six Sigma to actually exacerbate this problem by fostering analysis paralysis. Critiques of classic Six Sigma complain that it is too slow and that the "DMAIC" process has actually slowed down rather than accelerated progress. We advocate a modified version of DMAIC called Accelerated DMAI2C which combines the elements of speed with the analytical value of Six Sigma.
-
Establishing an Expectation of a Tangible ROI
All too frequently senior leaders fail to explicitly state an expected ROI from their investment. We recommend senior leaders need to establish and expectation of an ROI on all performance improvement resources and establish a systematic approach to measuring and validating results. While quality is always the number one goal, senior leaders should set the expectation that if we are improving wait times, delays, deployment of staff, eliminating redundancies and other forms of waste, then there should be tangible cost recovery. We advocate that finance should be involved from the start in validating results. Using this approach, we guarantee a tangible financial ROI due to the structure of the 100-Day Workout.